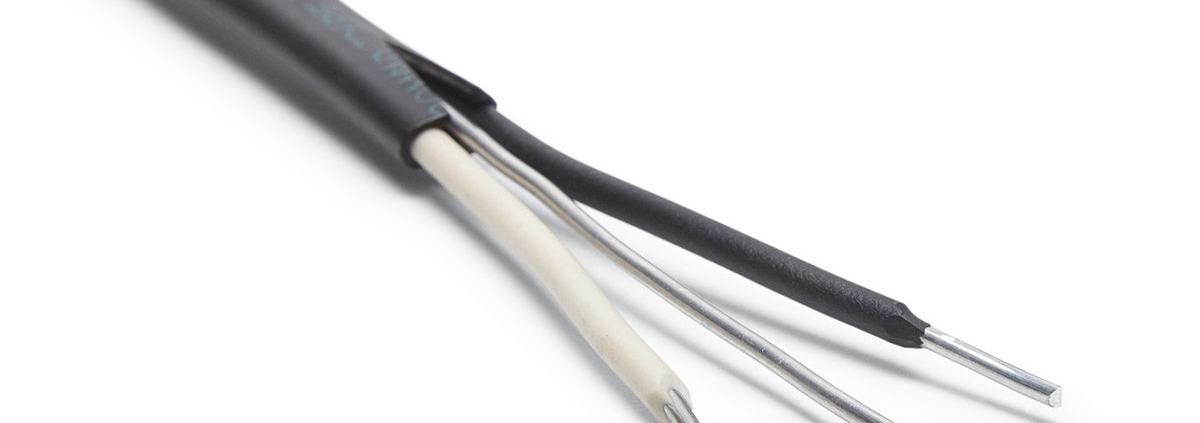
Dangers of Aluminum Wiring
Aluminum wiring was used primarily in the 1960s and 1970s, due to a scarcity of copper and as a way to save money and lower construction costs. However, a number of electrical fires have been attributed to aluminum wiring. Many building codes have been rewritten to not allow the use of single strand aluminum wire for branch circuit wiring in houses. It is important to note that multi strand aluminum wiring is considered safe and in use in most homes today in addition to copper wire.
Aluminum Wiring was used in the construction of roughly 1.5 million U.S. homes built between 1965 and 1973. According to a report published by the U.S. Consumer Product Safety Commission (CPSC), homes wired with aluminum wire manufactured before 1972 (“old technology” aluminum wire) are 55 times more likely to have one or more connections reach Fire Hazard Conditions than is a home wired with copper. This problem only gets worse with time. The aluminum-wired connections that fail tend to progressively deteriorate at a slow rate, and after many years can reach very high temperature while still remaining electrically functional in the circuits. A large number of connection burnouts have occurred in aluminum-wired homes. Many fires have occurred some involving injury and death.
Aluminum wire is widely regarded as a significant fire hazard. Installed in homes and mobile homes from the late 1960s through the early 70s, it is routinely disclosed by home inspectors and warrants careful attention whenever found.
Problems with aluminum wires occur primarily at the connections. Fittings often become loose, resulting in overheating, carbon build-up, and eventual fire inside the walls. Gradual melting and smoldering of the wire insulation may sometimes occur for a period of years before a fire actually ignites. Because of this, a detailed evaluation by a licensed electrical contractor is necessary to ensure that the entire electrical system is safe.
A proper evaluation includes an inspection of all connections in the breaker panels and at every outlet, switch, light fixture and junction box in the building. This is obviously a very time consuming-and therefore costly-process, but one which is obviously preferable to the risk of a fire.
A common misconception is the belief aluminum wiring must be replaced. This is an over-reaching solution to a problem that merely requires modification of the connections. A qualified electrician can upgrade the wire ends so that the problems associated with aluminum are sufficiently eliminated. For more specific details in this regard, consult a licensed electrical contractor.
Why Is Aluminum Wiring A Problem?
First, aluminum has a higher co-efficient of thermal expansion than copper. This means that when the wire heats up (as all wire does when electricity passes through) the aluminum tends to expand more than copper. This leads to the wire trying to move out from under the terminal screws. This phenomenon is called “creep” and can lead to poor connections and subsequent overheating.
Secondly, aluminum is softer than copper, and electricians used to working with copper would often nick aluminum wiring inadvertently. Nicking the wire, of course, reduces its diameter, and its ability to carry electricity safely. Localized hot spots can develop where the wire has been nicked. Further, if the wire is bent after it has been nicked it will often break.
Finally, the oxide of aluminum that forms on the wire is a very poor electrical conductor. All metals rust or oxidize to some degree. The greenish copper oxide that forms on copper wiring does not result in a problem. The oxide that forms on aluminum can lead to higher resistance and higher temperatures.
https://www.cpsc.gov/content/cpsc-safety-recommendations-for-aluminum-wiring-in-homes